Read about how Tiffany & Co. employed the metalworking technique of mokume-gane with illustrative artworks and process demonstrations, or watch the video below.
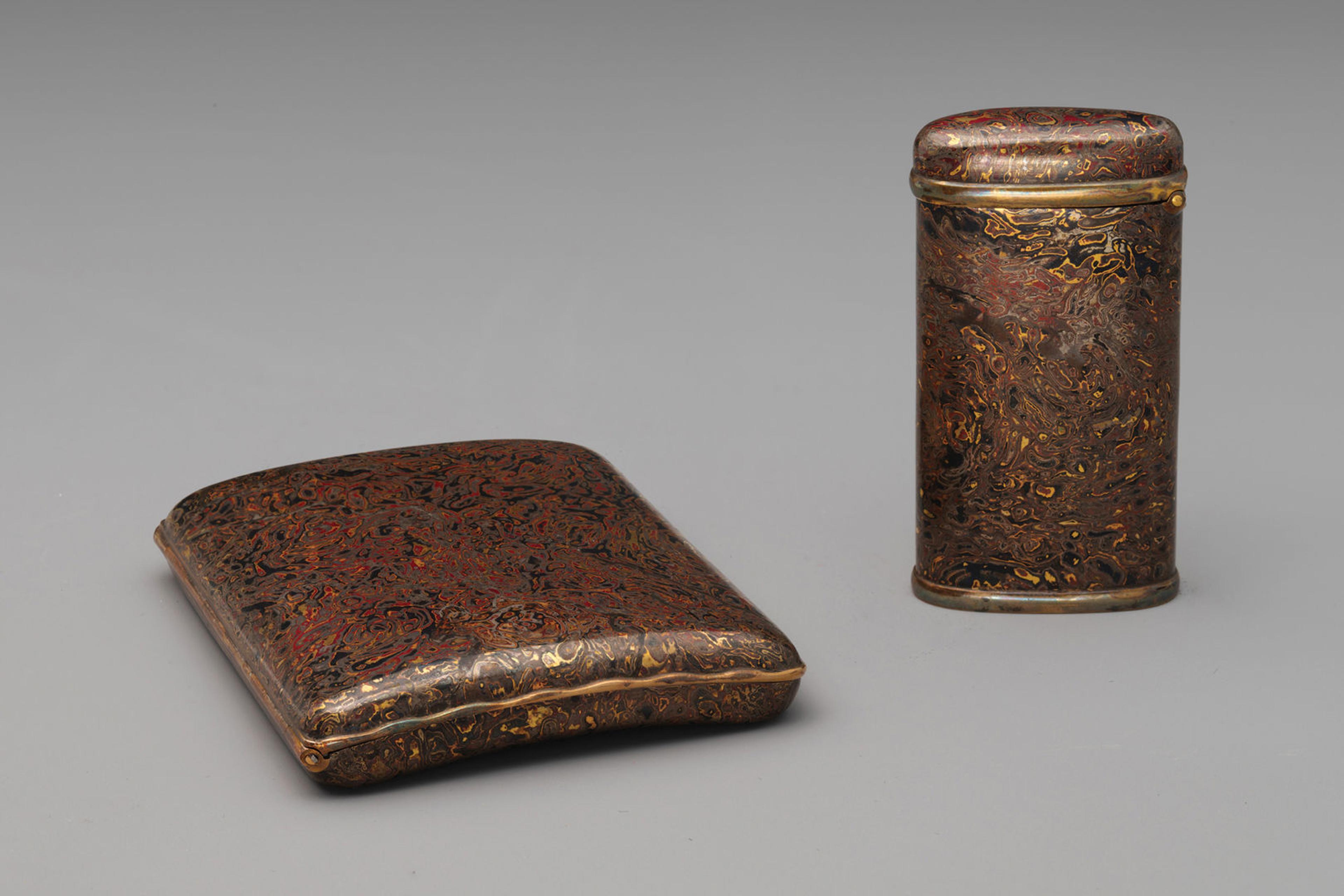
Tiffany & Co. (1837–present). Cigarette Case and Match Case, 1890–1900. Gold, silver, brass, patinated copper, gold-copper alloy, silver-copper alloy, and patinated copper-platinum-iron alloy, cigarette case: 3 x 2 3/8 x 5/8 in. (7.6 x 6 x 1.4 cm); match case: 2 3/8 x 1 1/4 x 5/8 in. (6 x 3.2 x 1.6 cm). The Metropolitan Museum of Art, New York, Gift of Susan Dwight Bliss (41.140.2-3)
Mokume-gane (pronounced moh-kuh-may gah-nay) is a Japanese metalworking technique by which layers of different metals are fused together with heat and pressure and worked to produce a patterned mixed-metal laminate. The term translates to “wood eye” or “wood grain metal.” In this process, Japanese metalsmiths so precisely control the heat and pressure applied to the various metals that the layers of the laminate fuse into a single billet. This technique is still in use today.
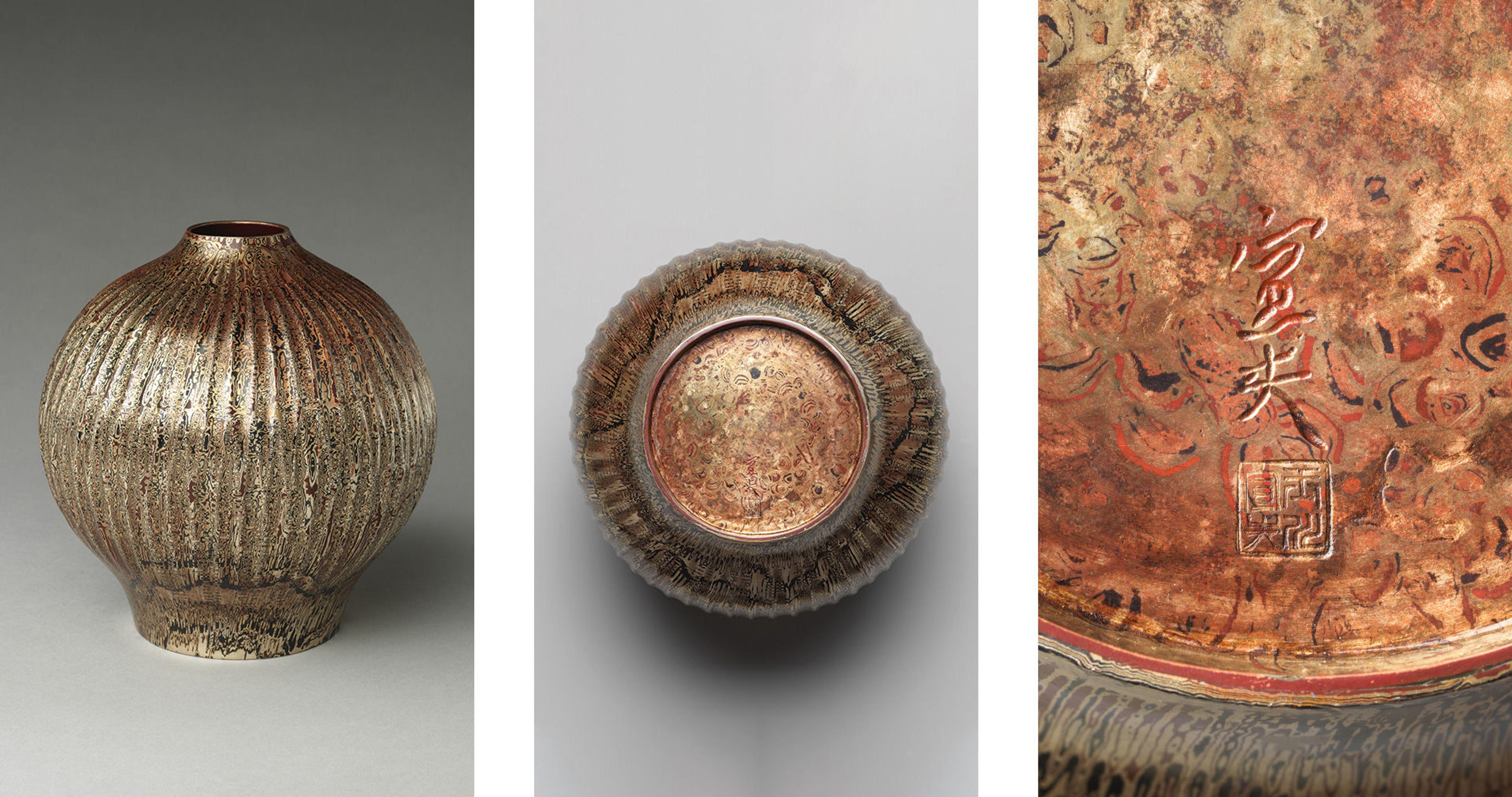
Tamagawa Norio 玉川宣夫 (Japanese, born 1942). Wood-Grain Metal Vase, 2019. Hammered silver, copper, and copper and gold alloy (shakudō), H. 8 1/2 in. (21.6 cm); Diam. 8 1/4 in. ( 21 cm). The Metropolitan Museum of Art, New York, Gift of Hayashi Kaoru, in celebration of the Museum’s 150th Anniversary, 2020 (2020.390.3). © Tamagawa Norio
Significant variation exists in how craftspeople have been able to achieve the swirling, patterned appearance, but many approaches involve carving into the stack to expose the various layers of different metals, and then compressing the stack with hammers. Another technique is hammering the material in order to create an uneven surface, then filing down the high points.
Edward C. Moore, the head of silver design at Tiffany & Co., collected decorative arts objects from throughout Asia, including many that feature mokume-gane. His collection was a source of inspiration—and impetus—for craftspeople at Tiffany & Co. to incorporate these patterns and aesthetics into the objects being produced at the firm. In their earliest attempts to emulate mokume-gane, they created inlays of contrasting metals and soldered them in place. Over time, these metalsmiths refined their technique, taking advantage of modern presses, kilns, and drills, and were able to successfully create bonded stacks that could be worked to create decorative objects.
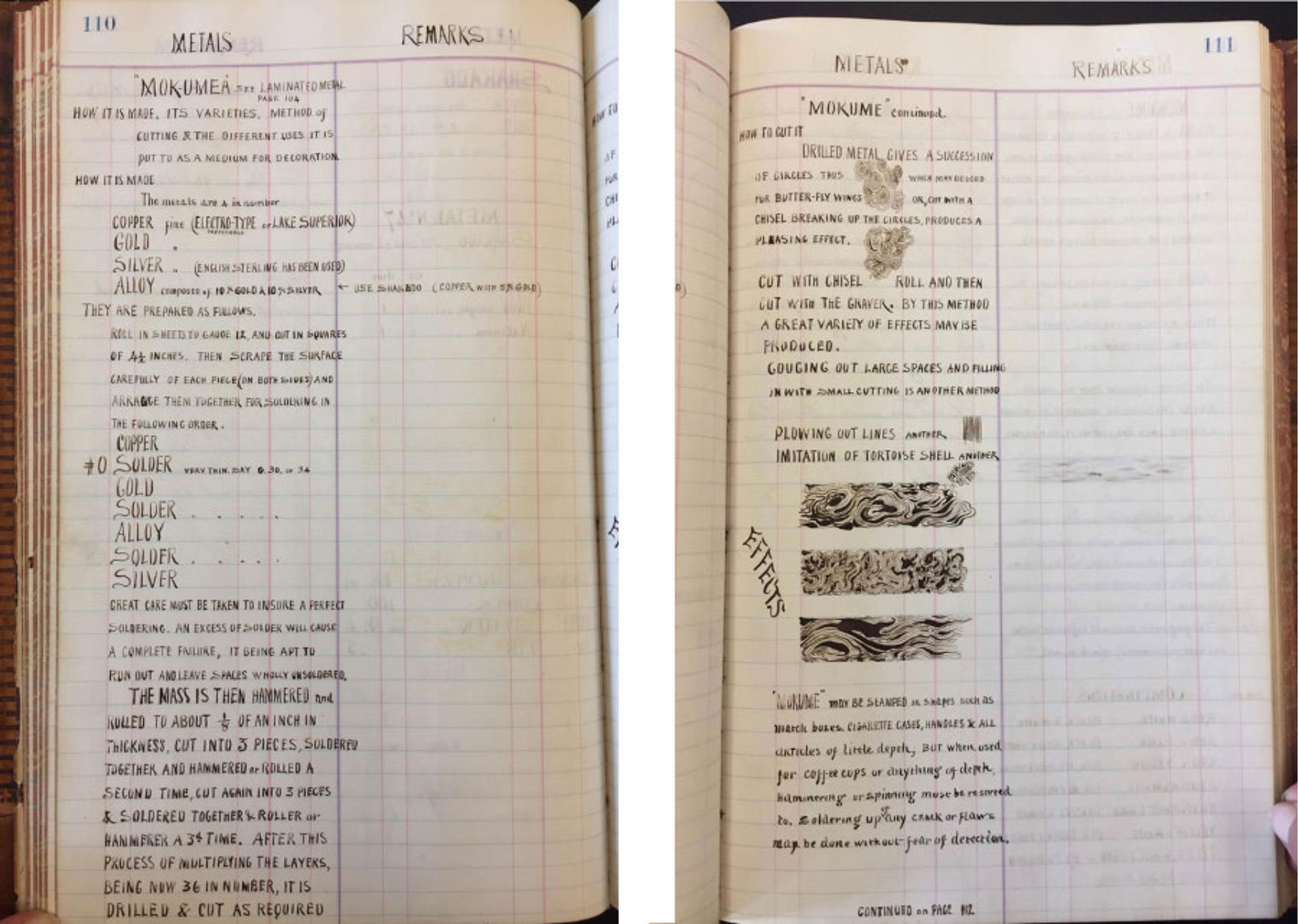
Tiffany & Co., Technical Manual, p. 110 and 111. Gorham Company Archive, John Hay Library, Brown University, Providence, Rhode Island
As noted in the excepts from the manual above, the technique was refined to include detailed instructions on how to drill and carve into the stack in order to achieve specific patterns with precision and accuracy.
The first step in an approach similar to that used at Tiffany & Co. is making a stack of alternating coupons (small squares) of different metals and/or alloys. Silver, gold, and copper are commonly used in this process. The stack below alternates silver and copper. Each coupon is prepared by abrading the surface with a scouring pad to remove any dust or grime that may prevent the layers of the stack from bonding.
Ground pumice is applied to the inside of a screw clamp to prevent the stack from sticking. The stack is then placed and secured within the clamp to hold the layers in alignment during pressing and firing.
A hydraulic press is used to compress the stack before it goes into the kiln.
Before the stack is placed in the kiln, flux (a paste of borax and water) is applied around the exposed outside edges. This creates a seal that will keep the stack from interacting with air and oxidizing while being heated inside the kiln.
The stack is placed in the kiln, where heat further bonds the layers.
As the stack heats, the metal expands, further compressing the coupons against each other in the clamp. This compression allows for the migration of atoms between the coupons while they remain in a solid state. The process, known as diffusion, bonds the individual coupons of the stack together so it can be worked without separating.
The modern process pictured differs from traditional Japanese mokume-gane, in which the mixed metal coupons in the stack are bonded through fusion. In fusion, the stack is heated to just above the melting temperatures of some of the component metals. While some of the metals are partially molten, local alloying occurs at the interface of the coupons. When the stack cools, it becomes a single billet. Achieving and controlling the temperatures to achieve fusion in non-electric kiln required significant experience and expertise, as well as technological innovation in both metalworking and kiln design.
The stack is removed from the kiln and left in the air to cool to room temperature.
Next, the stack is run through a rolling mill several times to compress it further The rolling mill uses two cylinders to apply pressure; as the bonded stack is run through, it lengthens.
In order to bring out the desired wood grain pattern, a drill is used to carve into the stack, revealing the lower layers of silver and copper. Chisels and other tool could also be used to achieve similar effects.
After drilling, the stack is run through the rolling mill repeatedly until the desired thickness and pattern are achieved.